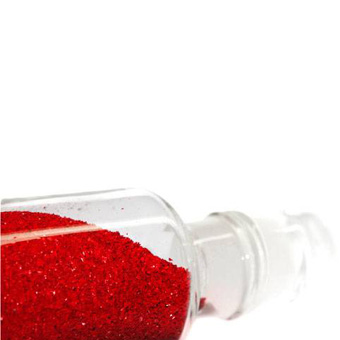
PVC Color Chip
Surface Printing for PVC sponge leather, PVC sheet, PVC film.
Jiuhlih Brand “CI-COLOR CHIP” series are used for printing from selected appropriate pigments, resins, and dispersants etc, through special technical process for forming small chips. These PVC pigment chips can be directly dissolved in organic solvents such as ketones and aromatic compounds.
High concentrations, with less quantity for use, no loss, high brightness, high adhesion, abrasive resistance, migration resistance, excellent dispersion, excellent diffusibility, excellent fastness, good quality and stability, measurement easily to make and precise, low cost for tinting, access convenience for handling and storage, and long period of storage.
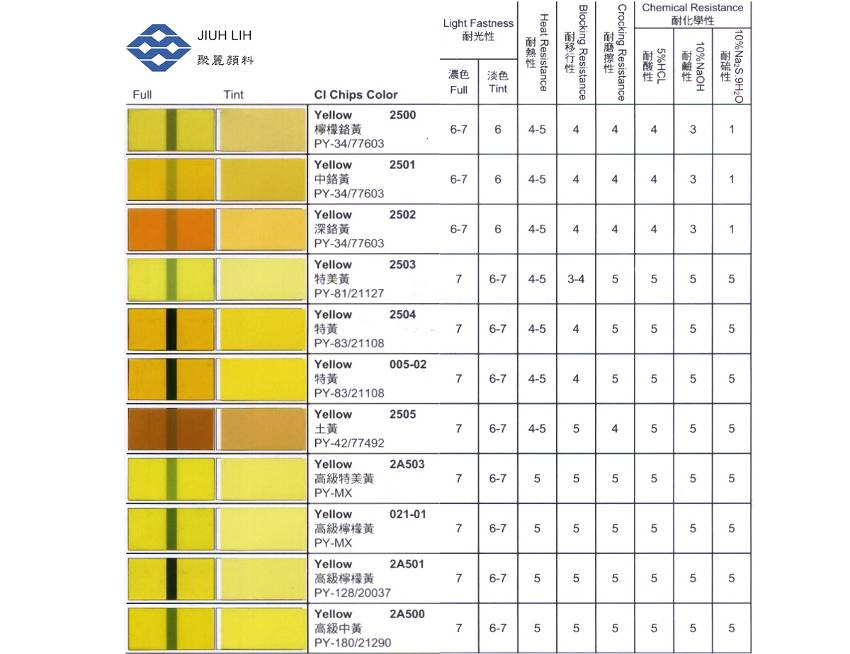
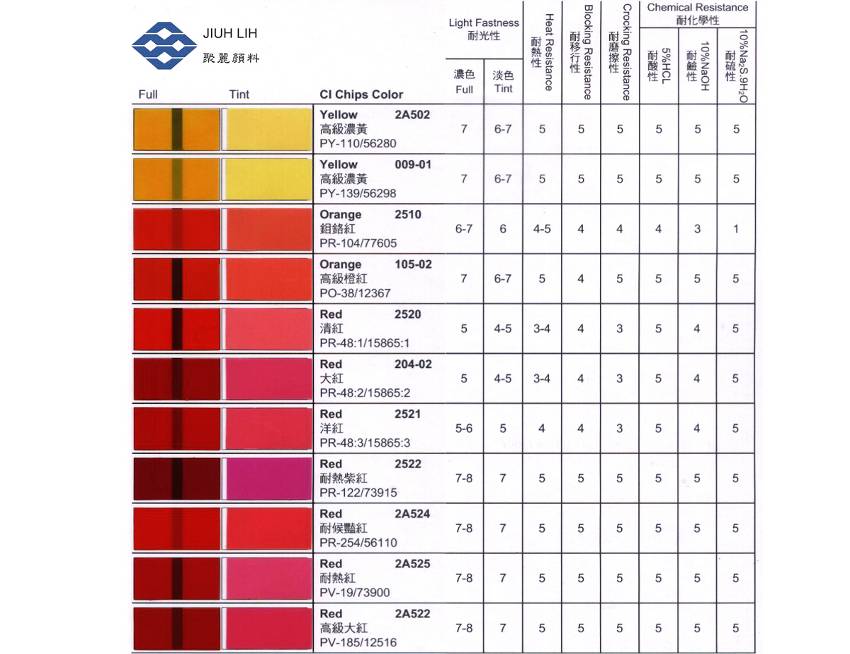
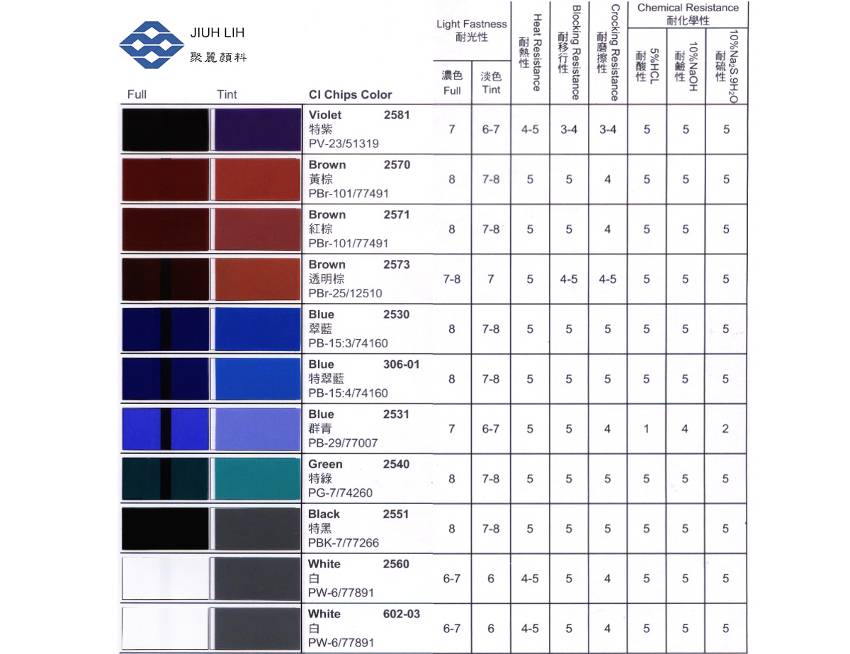
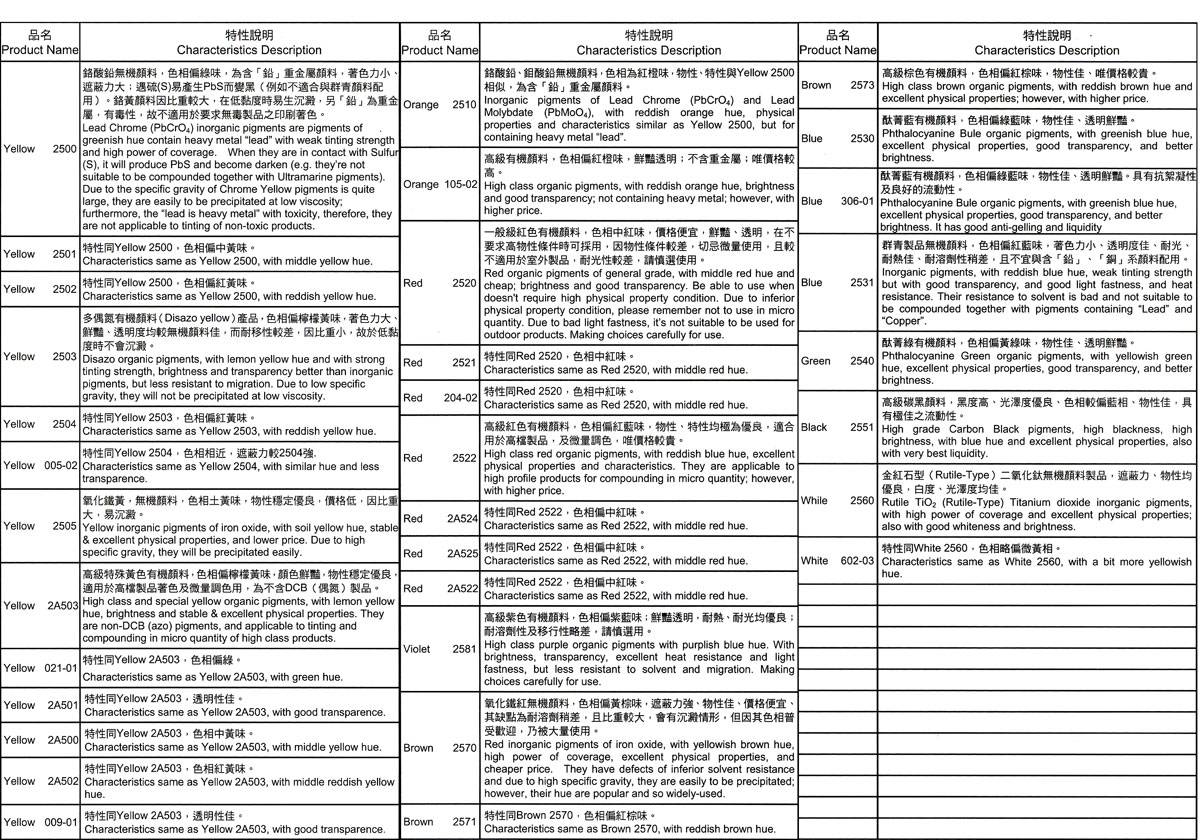
Due to different characteristics of CI-CHIP ingredients and various types of pigment, in the usage ratio of dissolution concentration and solvent ingredients are also different depending on their characteristics upon dissolving into the ink. The following dissolution ingredients provided are only for reference. Note: “Medium” is the carrier “Ink Oil (Ink Solvent)” used for increasing the viscosity.
Cl-Color |
Compound
|
Compound
|
|||
chip
|
solvent
|
chip
|
medium
|
solvent
|
|
Yellow 2500 |
25
|
75
|
25
|
10
|
65
|
Yellow 2501 |
25
|
75
|
25
|
10
|
65
|
Yellow 2502 |
25
|
75
|
25
|
10
|
65
|
Yellow 2503 |
12
|
88
|
12
|
20
|
68
|
Yellow 2504 |
12
|
88
|
12
|
20
|
68
|
Yellow 005-02 |
12
|
88
|
12
|
20
|
68
|
Yellow 2505 |
30
|
70
|
30
|
10
|
60
|
Yellow 2A503 |
12
|
88
|
12
|
20
|
68
|
Yellow 021-01 |
12
|
88
|
12
|
20
|
68
|
Yellow 2A501 |
12
|
88
|
12
|
20
|
68
|
Yellow 2A500 |
12
|
88
|
12
|
20
|
68
|
Yellow 2A502 |
12
|
88
|
12
|
20
|
68
|
Yellow 009-01 |
12
|
88
|
12
|
20
|
68
|
Orange 2510 |
30
|
70
|
30
|
10
|
60
|
Orange 105-02 |
12
|
88
|
12
|
20
|
68
|
Red 2520 |
15
|
85
|
15
|
20
|
65
|
Red 204-02 |
15
|
85
|
15
|
20
|
65
|
Red 2521 |
15
|
85
|
15
|
20
|
65
|
Red 2522 |
12
|
88
|
12
|
20
|
68
|
Red 2A524 |
12
|
88
|
12
|
20
|
68
|
Red 2A525 |
12
|
88
|
12
|
20
|
68
|
Red 2A522 |
12
|
88
|
12
|
20
|
68
|
Violet 2581 |
15
|
88
|
15
|
20
|
68
|
Brown 2570 |
30
|
70
|
30
|
10
|
60
|
Brown 2571 |
30
|
70
|
30
|
10
|
60
|
Brown 2573 |
12
|
88
|
12
|
20
|
68
|
Blue 2530 |
15
|
85
|
15
|
20
|
65
|
Blue 306-01 |
15
|
85
|
15
|
20
|
65
|
Blue 2531 |
30
|
70
|
30
|
10
|
60
|
Green 2540 |
15
|
85
|
15
|
20
|
65
|
Black 2551 |
15
|
85
|
15
|
20
|
65
|
White 2560 |
25
|
75
|
25
|
10
|
65
|
White 602-03 |
25
|
75
|
25
|
10
|
65
|
Anone (Cyclohexanone)
TOL (Toluene)
2. When the temperature is over 32°C, the optimal ratio of solvents: MEK : Toluene : Anone = 6 : 2 : 2 or 5 : 2 : 3
3. The evaporation rate of solvent are directly related with temperature and printing speed, so the adjustment of solvent ratio should consider the situation at that time to make appropriate adjustments.
4. The ink temperature should not exceed 40°C upon dissolving, otherwise it will affect their brightness and liquidity. CI-Black and Red should be paid by particular attention.
(2) Roter: NO:2 (for above 500cps NO:3)
(3) rpm (rotation speed): 62.5 rpm
(4) Room Temperature: Normal. Material Temperature: 26°C-34°C
Cut the plastic sheet or film, which is to be tested, into 5cm by 3.5cm; and cut the white clipping cloth into 6cm by 6cm. Put the surface to be printed against the white clipping cloth, stacking them up face-to-face; then clip them with plain glasses. On top, placing a heavy hammer weighing 120g/cm2, and put them into the oven at 50°C±2°C for 5 hours. After that, take them out of the oven, idling for 5 minutes. Tear down the white (black or transparent) plastic sheet from the printed plastic sheet which is to be tested, then determine the levels by visual observations according to the symptom of color migration. Normally, it will be determined into level 1-5; level 1 means Very Poor (worst color migration), and for level 5, Very Good (no influence).
(2)Testing for Sulfur Resistance: Take a piece of post-printed plastic sheet (film) from item 1, and place them on the top of a H2S generator. After pressing for 15 minutes with flat glass on the top, then take them out to assess their degree of color fading. On a comparison Scale 1-5, Number 1 is the worst (color is changed severely), while Number 5 is the most excellent (color will not be changed).
1.Light Fastness
Scale
|
Result
|
8
|
Outstanding
|
7
|
Excellent
|
6
|
Very Good
|
5
|
Good
|
4
|
Fairty Good
|
3
|
Poor
|
2
|
Poor
|
1
|
Very Poor
|
2.Scale of Heat Resistance, Migration, Resistance to Acids or Alkalis, and Resistance to Sulfur.
Scale
|
Result
|
5
|
Very Good
|
4
|
Good
|
3
|
Fairty Good
|
2
|
Poor
|
1
|
Very Poor
|