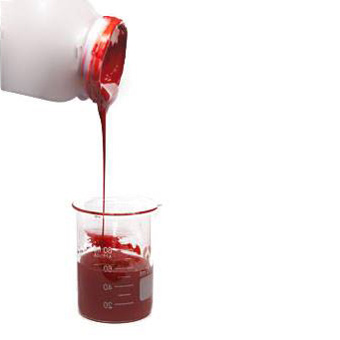
PVC Color Paste
Model:VP series
Main Purpose
Paste moulding for PVC casting and dipping etc., or coloration for PVC semi-rigid artificial leather.
Add to inquiry
Paste moulding for PVC casting and dipping etc., or coloration for PVC semi-rigid artificial leather.
Product Introduction
Jiuhlih Brand PVC Color Paste (VP-Paste Color) is offered by specially selected pigments of excellent grades plasticizers, resins, dispersants and processing additives etc., then by grinding and dispersing with mechanical facilities to become a paste formed pigment.
Features & Benefits
The PVC Color Pastes of this series have a very high concentrated tinting strength, best dispersion ability, high stability, and are easy to be produced only requiring a little stirring.
Catalog
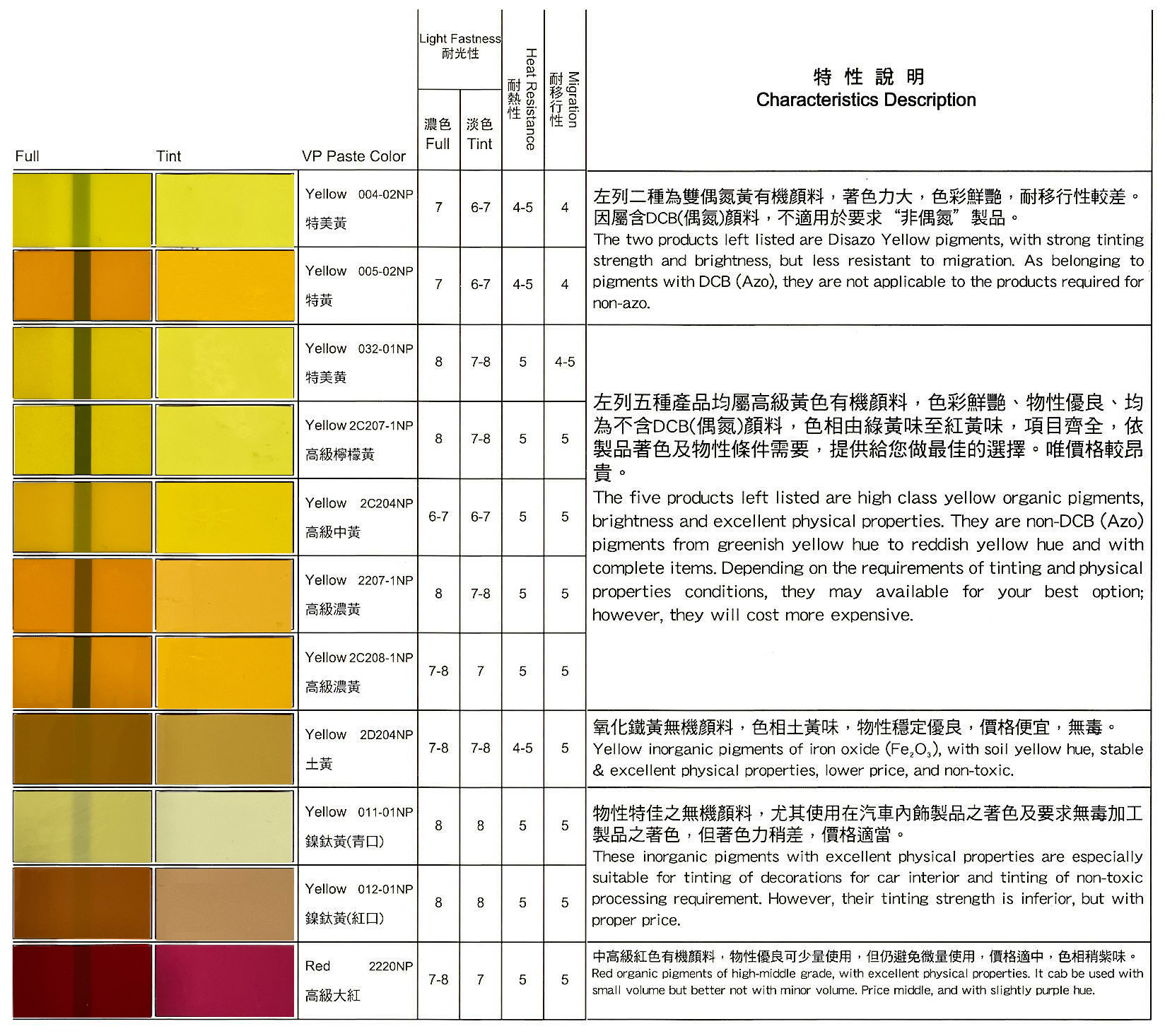
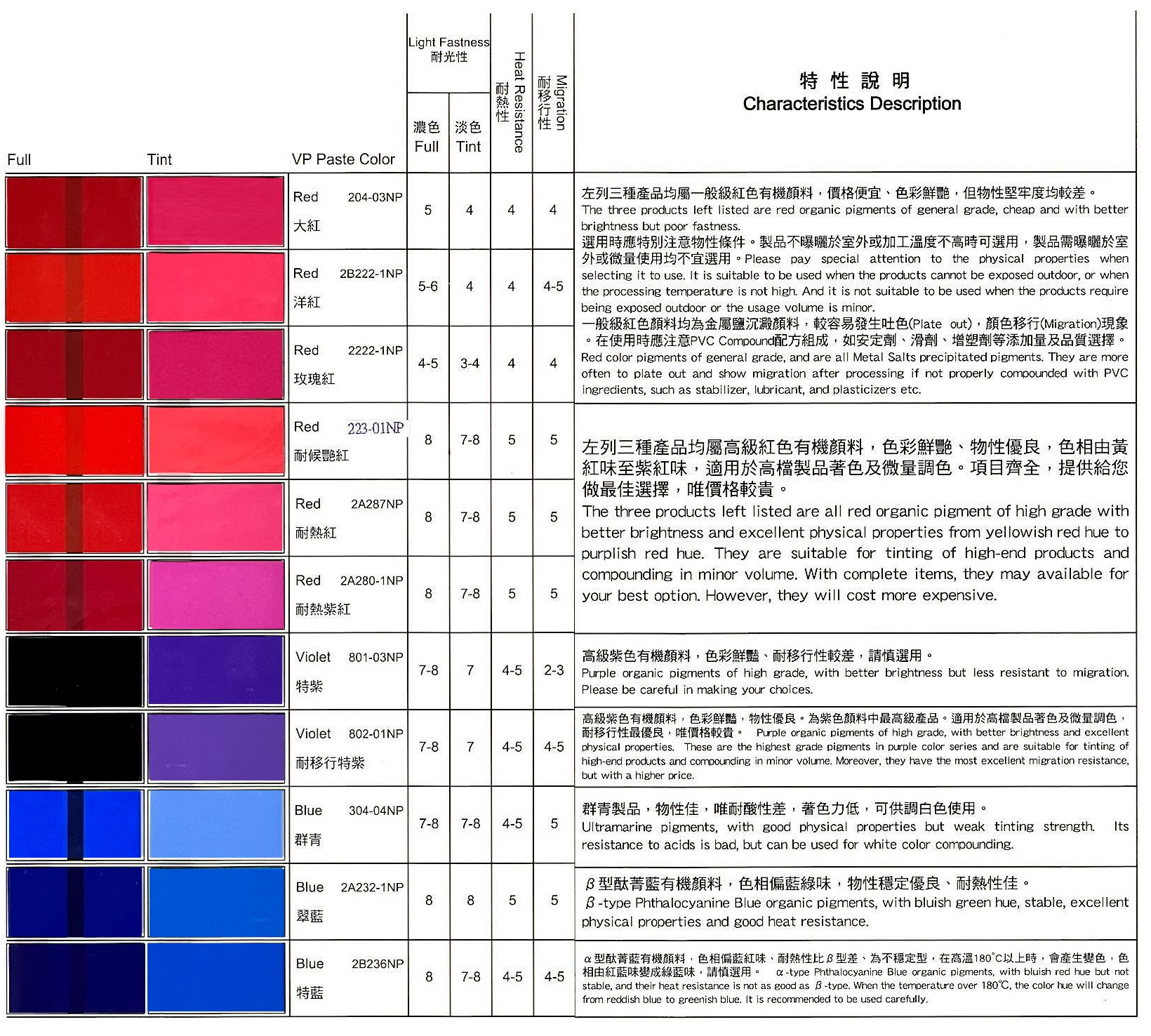
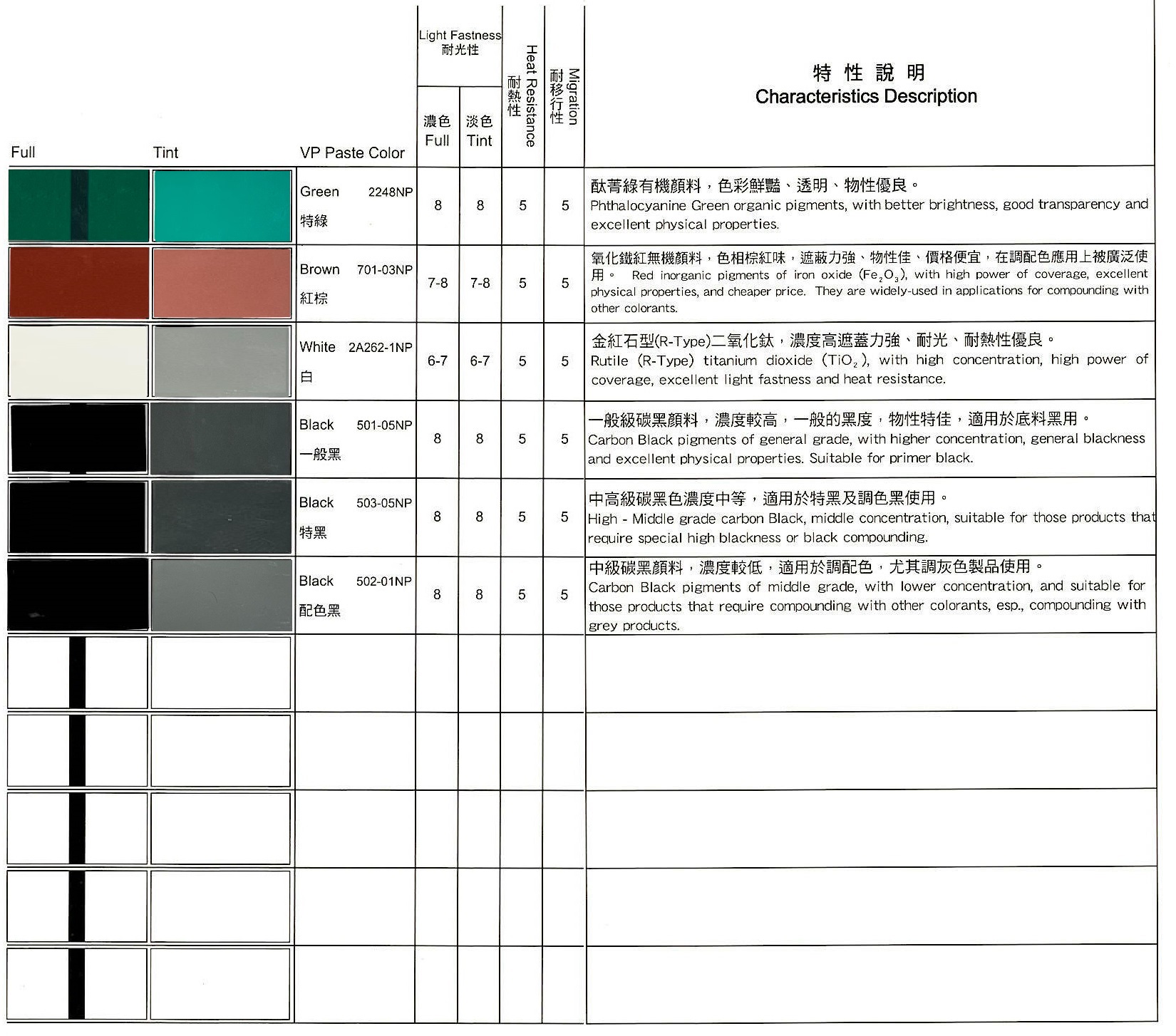
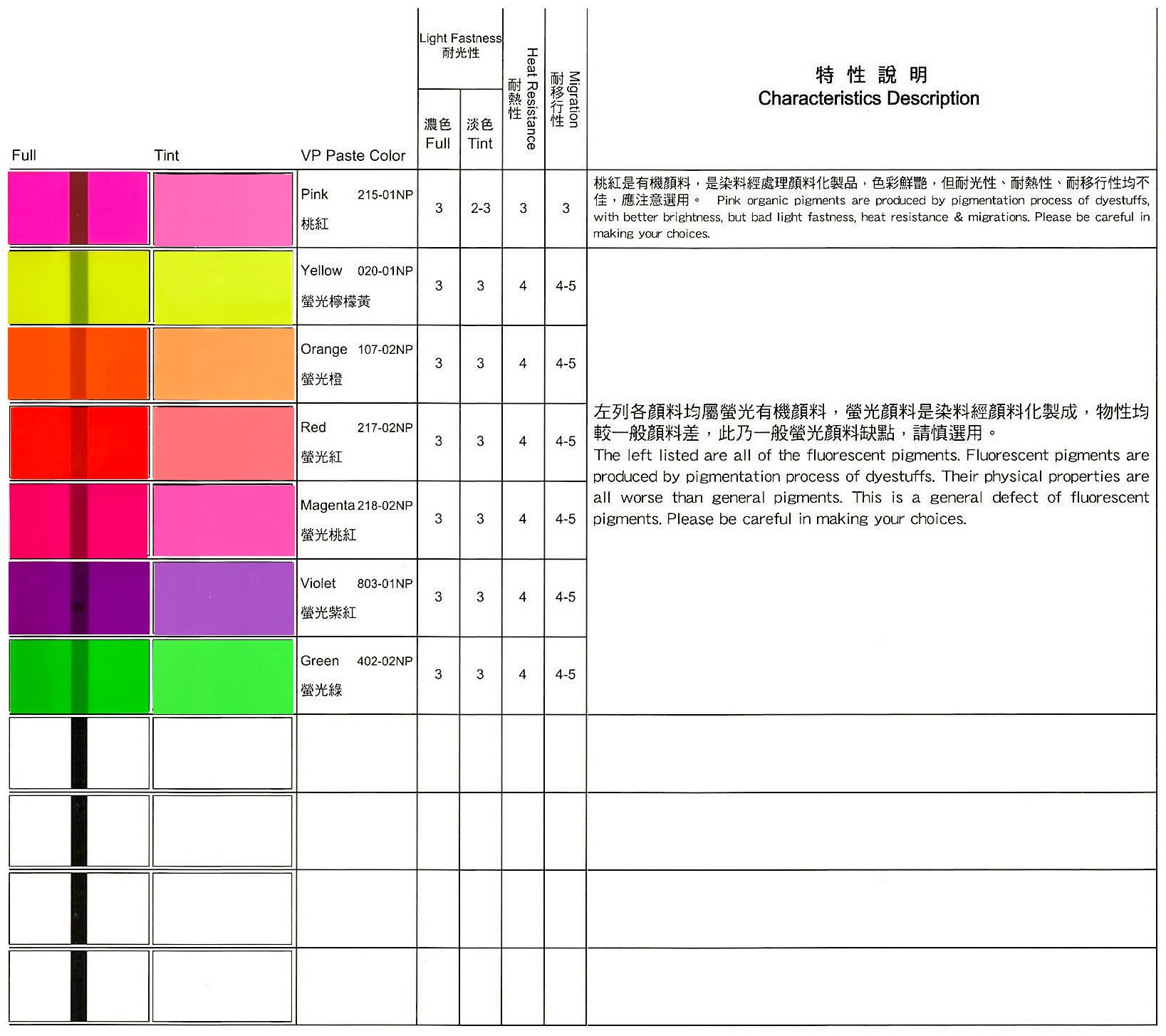
Color pattern sheets
Compositions of PVC Compound
Full Shade
Tint Shade
Materials
|
General(Compound)
|
Foaming(Compound)
|
PVC Paste Resin
|
100
|
100
|
Plasticizer
|
80
|
90
|
C.Z Stabilizer
|
2.5
|
2.5
|
Epoxidized Soybean Oil
|
1.0
|
-
|
Foaming Agent
|
-
|
3.0
|
Filler
|
-
|
20
|
Full Shade
|
With color
|
White
|
Black
|
Fluorescent
|
General(Compound)
|
100
|
100
|
100
|
100
|
PVC Color Paste(VP Color)
|
2
|
4
|
1
|
4
|
|
||||
Foaming(Compound)
|
100
|
100
|
100
|
100
|
PVC Color Paste(VP Color)
|
5
|
10
|
2.5
|
10
|
Tint Shade
|
With color
|
White
|
Black
|
Fluorescent
|
General(Compound)
|
100
|
100
|
100
|
100
|
VP Color
|
2
|
4
|
1
|
4
|
Wihte 2260
|
4
|
-
|
4
|
4
|
Black 2254
|
-
|
0.16
|
-
|
-
|
Conditions of Color Pattern
General:
Coating Thickness 0.6mm
Drying Temperature 150ºC X 60 Sec
Drying Temperature 150ºC X 60 Sec
Foaming:
Coating Thickness 0.35mm
Foaming Temperature 210ºC X 70 Sec
Foaming Temperature 210ºC X 70 Sec
Method of Testing for Physical Property
Testing of Light Fastness:
Take pieces of general color pattern sheets to put them into the Fade-o-Meter for light exposure. Afterward, take out the test pattern sheets to assess their degrees of light fastness against a standard Blue Scale which is assigned to value from 1 to 8. Level 8 is the outstanding (color will not be changed) and Level 1 is very poor (color is changed severely).
Testing for Heat Resistance:
Take pieces of general color pattern sheets and put them into an oven under a condition of 180℃ ± 2℃ for 30 min. Then take out the test pattern sheets to inspect their degree of color changing (degree of color fading). Afterward, assess the results for their degrees of heat resistance against a standard Gray Scale which is assigned to value from 1 to 5. Level 5 is the most excellent (color will not be changed) and Level 1 is the worst (color is changed severely).
Testing for Migration:
Take pieces of general color pattern sheets sandwiched in between two pieces of white color pattern sheets, and put the whole structure into an oven under a loading pressure of 3KG on the top for 80°C x 24 hours. Then take them out finally to inspect the degree of migration on the white color sheets surface against a Scale which is assigned to value from 1 to 5. Level 5 is the most excellent (no migration) and Level 1 is the worst (severe migration).
Testing for Acids or Alkalis Resistance:
Take pieces of general color pattern sheets and dip it into the bath of 5% HCI or 10% NaOH for 24 hours. Then take out the test pattern sheets to inspect their degree of color changing against a Scale which is assigned to value from 1 to 5. Level 5 is the most excellent (color will not be changed) and Level 1 is the worst (color is changed severely).
Testing for Sulfur Resistance:
Take pieces of general color pattern sheets and place them on the top of a H2S (Hydrogen Sulfur) generator. Then cover them with a flat piece of glass on top for pressing for 15 minutes. And then take out the test pattern sheets to inspect their degree of contamination against a Scale which is assigned to value from 1 to 5. Level 5 is the most excellent (was not contaminated at all) and Level 1 is the worst (was contaminated severely).
Scale for assessment of physical property of pigment
1.Light Fastness
Scale
|
Result
|
8
|
Outstanding
|
7
|
Excellent
|
6
|
Very Good
|
5
|
Good
|
4
|
Fairty Good
|
3
|
Poor
|
2
|
Poor
|
1
|
Very Poor
|
2.Scale of Heat Resistance, Migration, Resistance to Acids or Alkalis, and Resistance to Sulfur.
Scale
|
Result
|
5
|
Very Good
|
4
|
Good
|
3
|
Fairty Good
|
2
|
Poor
|
1
|
Very Poor
|
※Remark: The Scale of Fastness for comparison is very important in the proper selection of appropriate pigments for coloring processes. Conditions of processing, end-uses application fields and the required properties of the finished product should be consulted before making a final selection of the optimal pigments.
Please contact us for further assistance